Ez a német üzem adhat példát a hazai iparvállalatoknak
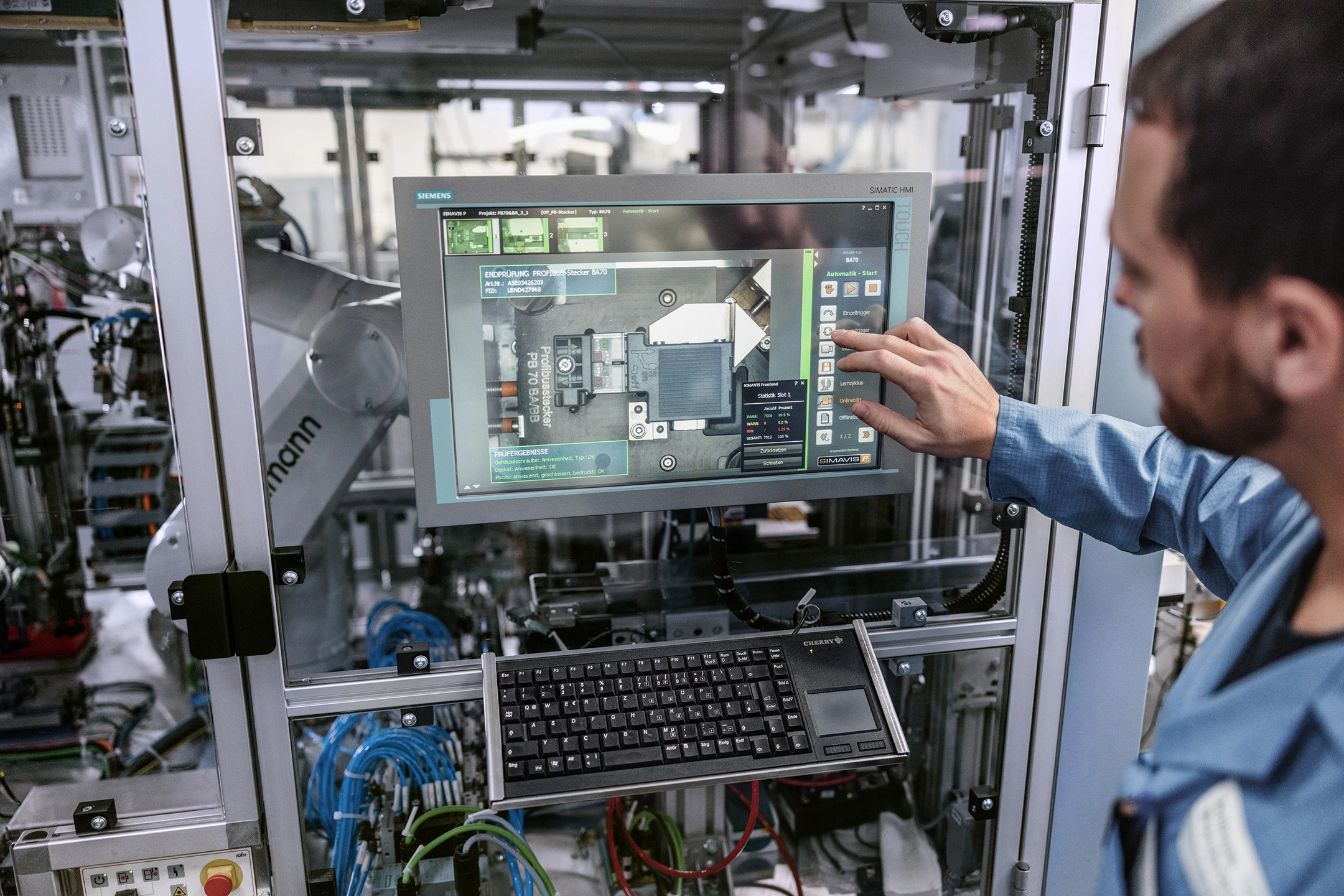
Az egyik ilyen, frissen kitüntetett gyár Németországban, a bajorországi Fürth-ben található. Itt a termelőüzem energiafogyasztását modern eszközök bevetésével 64 százalékkal csökkentették, 72 százalékkal mérsékelték az egy egységnyi termelésre vetített a szén-dioxid-kibocsátást, miközben 145 százalékkal emelkedett a gyár termelékenysége. Ez már nem az első Siemens-gyártóegység, amit mintagyárként ismernek el: a németországi ambergi és erlangeni, illetve a csengtui (Kína) üzem is elnyerte már ezt a díjat.
Fókuszban az energiahatékonyság
Az 1954-ben alapított fürth-i telephelyen mintegy 1700 munkavállaló dolgozik ipari automatizálási termékek fejlesztésén és gyártásán. Itt készülnek például a SIMATIC HMI érintőképernyős ipari kijelzőpanelek, amelyek világszerte irányítópultként szolgálnak a gyártási folyamatok során.
A telephely már 2026-ban el tervezi érni a nettó zéró kibocsátást, ami négy évvel előzheti meg a Siemens globális vállalati célkitűzéseit. Ezért itt már 2012-ben létrehoztak egy interdiszciplináris fenntarthatósági csapatot, akik szisztematikus intézkedéseket vezettek be az energiafogyasztás és a CO₂-kibocsátás csökkentésére. Emellett 2019 és 2023 között az üzemben az ipari hulladék egységnyi termelésre vetített mennyisége is csökkent 47 százalékkal.
Ezeknek az energiahatékonysági intézkedéseknek a középpontját egy, az épületek és a gyártás energiahatékonyságának javítását célzó program jelenti. A telephelyen több mint 350 mérőeszköz gyűjti a teljesítményadatokat, ami az energiafogyasztás célzott csökkentést teszi lehetővé az egységes működő szoftvereknek köszönhetően.
A rendszer konkrét fejlesztéseket is képes automatikusan javasolni a további megtakarítási lehetőségek kiaknázásához. Ennek köszönhetően például a világítási rendszereknél 952 MWh (megawattóra), az épületautomatizáció terén pedig 103 MWh energiát takarítottak meg, ami hozzávetőlegesen 2 ezer háztartás éves villamosenergia-fogyasztásának felel meg. A megtakarítási eredmények a legyártott termékek karbonlábnyomán is meglátszanak, amelyet a mérőeszközök által gyűjtött adatok alapján, pontosan ki tudnak számítani; – ehhez pedig az esetek 90 százalékában a Siemens erre a célra kifejlesztett, SiGREEN szoftverét használják.
Modernizált hálózatok és körforgásosság
A villamoshálózati incidensekből (például az időjárás vagy túlterhelés okozta áramkimaradásokból) eredő energiaveszteségeket egy elektromágneses szűrőrendszer kialakításával minimalizálják a telephelyen. Ezzel a 2019 és 2023 közötti vizsgált időszakban az összes áramfogyasztás 3,8 százalékát tudták megtakarítani, valamint ezáltal stabilabbá vált az energiaellátás, és csökkent a leállások kockázata is.
Az ipari hulladék csökkentésére továbbá körforgásos szemléletet alkalmaznak. A helyszínen működik egy javítóüzem is, amelynek segítségével már 310 különböző termék élettartamát sikerült meghosszabbítani, ez a szám pedig 2026-ra várhatóan 2 ezerre emelkedik majd. Így, a termékek hosszabb élettartamából adódóan, karbonlábnyomuk is csökken, ráadásul az üzem megspórolja a selejtezés és az új termék gyártásából adódó CO2-kibocsátást is.
Karbonmentesítés
Mindemellett további intézkedésekkel is csökkentik a telephely energiafogyasztását, növelve az erőforrás-hatékonyságot, és ösztönözve az önellátóvá válást. 2023 őszén például egy 3300 négyzetméteres napelemes rendszert telepítettek a parkolóház tetejére, amely 460 kWp (kilowatt-peak) csúcskapacitással rendelkezik. Összehasonlításképp: egy átlagos háztartási napelemes rendszer 2-5 kWp csúcskapacitással üzemel. Ez egyébként az egyik legnagyobb ilyen rendszer, amit Siemens-létesítményen elhelyeztek.
Emellett a gyár a nitrogént is helyben állítja már elő a gyártási folyamatok, például a hegesztési eljárások kiszolgálására, így 2024-től már nincs szüksége nitrogénszállítások fogadására sem. Az ipari folyamatokból származó hulladékhőt pedig az épület fűtésére használják.